Skyloft Multi-unit development
Skyloft Multi-unit development featuring Oblique™ Weatherboard & ExoTec™ Facade Panel
“For apartment buildings, it’s important to minimise the maintenance on the exterior walls.”
Purpose-built to meet the needs of first home buyers, the Skyloft multiunit development utilised three products from James Hardie to achieve its cost and durability objectives.
Skyloft in Burns Avenue, Takapuna, is an excellent example of how responsible residential development can create attractive homes to address an urgent market need. In this case, affordable smaller homes for first home buyers in the Auckland market. Xinwei Gu, the architect for the project, was excited to be making a difference for an important group of home buyers.
“The intention of Skyloft was to provide more small-sized homes instead of larger multi-unit terrace houses, in order to minimise the cost per household and meet the demands of first-time homebuyers.”
To stay within project budget without compromising the quality and longevity of the structure, Xinwei designed the building using prefabricated steel columns and beams, a composite steel deck and concrete floor systems. From the outset, his preferred cladding was James Hardie’s fibre cement cladding products.
Material selection
“Compared to other claddings that offer a similar performance, such as aluminium cladding, James Hardie’s fibre cement products have a reasonable cost, making them more accessible to developers and homeowners.
Specifying James Hardie’s cladding also assisted with fire safety compliance. “As the building didn’t need a fire sprinkler system, fire aprons were designed on the exterior walls between each floor to meet the fire protection regulations. This approach necessitated the use of a lightweight, non-combustible cladding system, which James Hardie was able to provide.”
Low-maintenance and stability were two other reasons for selecting James Hardie’s claddings, in this case Oblique™ Weatherboard and ExoTec™ Facade Panel. Fibre cement claddings aren’t affected by temperature change, can be painted a large variety of colours (including dark shades) and require minimal maintenance.
“For apartment buildings, it’s important to minimise the maintenance on the exterior walls. The low maintenance requirements of James Hardie’s claddings make them an excellent choice for this purpose.”
Another Hardie™ fibre cement product that assisted the Skyloft project was RAB™ Board pre-cladding, an all-in-one bracing, airtight and fire resistant fibre cement sheet. “The RAB™ Board product allows the interior construction work to begin before the exterior cladding is installed, speeding up the overall process and reducing cost.”
Technical Support
During the design phase of Skyloft, Xinwei accessed James Hardie’s comprehensive specification system and detail library. These resources allow designers to fully understand product performance and construction requirements. They also make it easier for building consent authorities to approve technical drawings.
“For Skyloft I didn’t need to contact James Hardie for technical support, because everything I needed was available online. For other projects we have called on James Hardie’s technical support – they reply to our emails and provide guidance over the phone. We’re always happy with the level of support we receive.”
Location
Featured Products
Project Type
Industry Professionals
Designed by Xinwei Gu of WDA Studio and built by V-Pro Construction
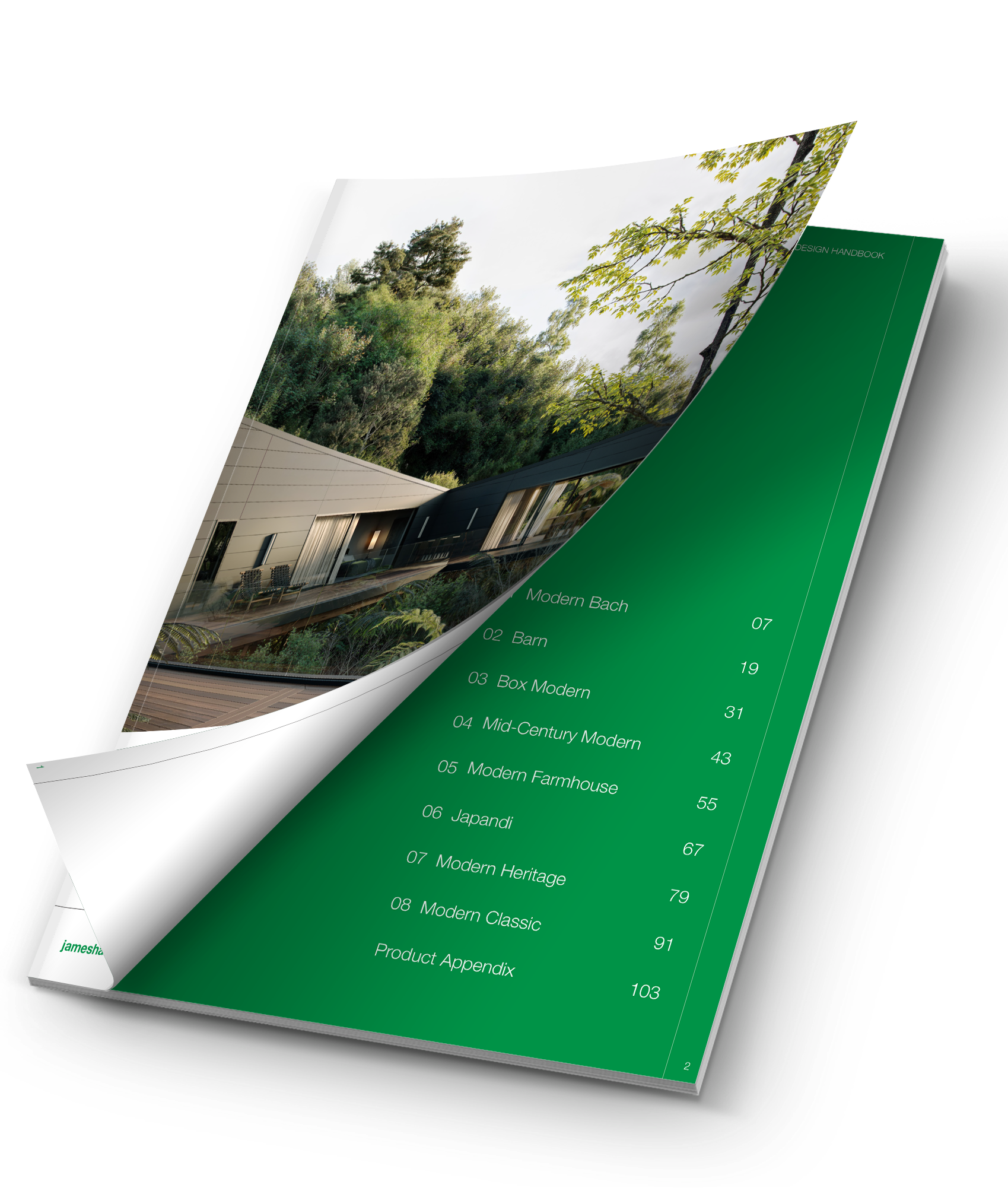
The Design Handbook
The Hardie™ Cladding Collection has a wide variety of products to select from, creating design versatility, in which It’s Possible™ to Make Modern™ like never before. It’s a movement that’s reshaping perceptions and changing the way New Zealand builds. Whether you are planning a renovation, new build, or extension, this forecast will be an invaluable tool on your journey. Welcome to the James Hardie Design Handbook. It's time to Build Your Modern Life.